4. Испытания и интерпретация результатов испытаний
Эластомерные материалы отличаются от других материалов не только тем, что они "эластичные", они отличаются по комплексу своих свойств. Такие привычные в технике понятия, как твердость или предел прочности при растяжении, должны интерпретироваться иначе. Кроме того появляются новые свойства, такие как сопротивление старению или скорость деформации. Едва ли они являются постоянными величинами. Большинство свойств сильно зависит от температуры и других внешних воздействий, а некоторые даже от величины и формы испытуемых образцов или фасонного изделия. Существует большое количество синтетических каучуков и еще большее число их композиций. Тем не менее, возможность комбинаций материалов тоже ограничена. Например, в NBR невозможно соединить максимальную маслостойкость с оптимальным поведением при низких температурах. По физическим и химическим причинам некоторые свойства вообще не связаны друг с другом. Если одно из свойств меняется, то это совсем не значит, что поменяются и другие. Это может быть как преимуществом, так и недостатком для определенных задач. С учетом вышесказанного, при предъявлении технических условий следует избегать излишних требований. Такой подход обеспечит целенаправленный выбор материала для конкретного применения.
4.1 Физические свойства
• твердость Твердость является наиболее часто используемым параметром для характеристики резино-эластичных материалов. Испытания проводятся на измерительных приборах по Шору A, D и IRHD. Эластомерные материалы Simrit, в основном, измеряют по шкале Шора А. Измерения в испытательной лаборатории проводятся по DIN 53 505. Твердость по Шору может быть также измерена портативным прибором. При этом, правда, часто не исключается неточность измерений. Тем не менее, во многих случаях получаются полезные относительные или сравнительные значения, если следовать стандартной процедуре и если при измерениях принимать во внимание следующее: Образец слишком малой толщины дает завышенное значение. То же действует для высоких контактных давлений. Наоборот, измерения, выполненные слишком близко к краю, например, с фасонными изделиями очень малого размера, дают заниженные значения.
|
|
Испытуемые образцы должны быть по возможности более плоскими, плотно прилегать к поверхности. Всегда располагайте образец параллельно измерительному инструменту, точно соблюдайте время измерений. Другой метод измерений в лаборатории заключается в определении твердости резины по международной шкале (IRHD; DIN ISO 48): измеряется глубина проникания определенного шарика при определенной нагрузке. Для высокоэластичных материалов значение IRHD соответствует примерно твердости А по Шору. Для материалов, в которых возможна пластическая деформация, значения, полученные двумя методами, могут значительно расходиться. Вариант этого метода с использованием шарика малого диаметра (0,4 мм) дает возможность проводить измерения на маленьких и тонких образцах (т.н. «микротвердость» по DIN ISO 48 методика M). Поэтому он часто применяется для измерений на готовых деталях. При использовании этого метода, кроме расхождений, связанных с различными способами измерений, необходимо учитывать дополнительные факторы, зависящие от поверхности образца (неровности, например, вследствие шлифовки, искривления, объясняющиеся геометрией изделия, отвердение поверхности, коэффициент трения), которые могут привести к еще большим расхождениям значений замеров. Значения, полученные на готовых деталях, как правило, не соответствуют значениям на стандартных опытных образцах. Поэтому при указании твердости всегда следует указывать и метод измерений каким она была установлена например, твердость 80 по Шору A или твердость 72 IRHD. Чтобы предотвратить разногласия между между заказчиком и поставщиком, следует точно договориться о методике испытаний на твердость готовых продуктов. Как правило, значение твердости дается с допуском ±5. Этот, относительно большой, диапазон необходим, чтобы учесть разницу между различными приборами и контролерами, а также неизбежный разброс значений при изготовлении.
• Напряжение и модуль упругости Как твердость, так и напряжение, и модуль упругости являются параметрами деформации эластичных материалов. Значение напряжения, полученное при испытании на растяжение согласно DIN 53 504, при растяжении 100 или 300% определяется как сила, необходимая для возникновения относительной деформации, деленая на первоначальное сечение образца. Напряжение часто неправильно называют "модулем". Модуль упругости или модуль удлинения – это значение напряжения, поделенное на относительное изменение длины (удлинение). Эта величина у резино-эластичных материалов непостоянна. Закон Гука σ = E ⋅ ε, по которому напряжение σ пропорционально удлинению ε, причем модуль упругости E является постоянной величиной, действует для резины только
|
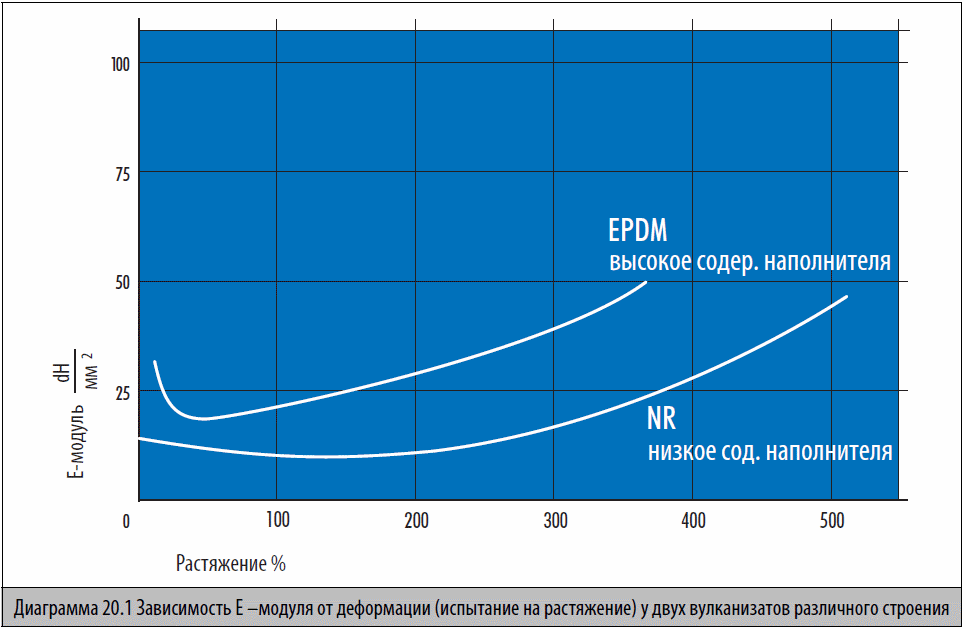
|
в ограниченном диапазоне деформаций. Этот диапазон может быть различным для разных материалов. Модуль упругости может при удлинении как увеличиваться, так и уменьшаться →Диаграмма 20.1. Модуль упругости зависит от, так называемого, фактора формы, который представляет собой отношение площади нагруженной поверхности к свободной поверхности детали или образца. При этом под нагруженной поверхностью понимают поверхность растяжения или давления (без противоположной поверхности), а под свободной поверхностью – сумму всех поверхностей, где тело может свободно расширяться или сжиматься. Обе поверхности измеряются в ненагруженном состоянии. Так, напр., фактор формы F для аксиально нагруженного цилиндра
F = d/4h (d = диаметр, h = высота).
• Другие модули Для деформации также имеют значение другие модули. Модуль сдвига или скольжения и динамические модули важны для колебательных процессов. Они здесь детально не рассматриваются. Методики тестирования установлены в DIN 53 513, DIN 53 445 и ASTM 945 (тест Ерцли).
|
|
• Соотношение параметров различных деформационных свойств После всего сказанного можно ожидать только приблизительную взаимосвязь между отдельными параметрами. Модуль сдвига G и модуль упругости E имеют приблизительные значения для резино-эластичных материалов:
G = 1/3 E.
Между твердостью по Шору A или IRHD и модулем упругости при 5–10%-ной деформации давлением существует приблизительная зависимость, которая представлена на диаграмме →Диаграмма 20.3. При больших деформациях твердость не зависит от модулей, даже если у материала при увеличении твердости модули растут. Для всех деформационных свойств характерно то, что они сильно зависят от температуры и времени. Зависимость от времени означает, что скорость деформации (напр., скорость растяжения при испытании на растяжение или частота в динамическом модуле) и время снятия измерения (напр., при измерении твердости) входят в измеряемую величину.
|
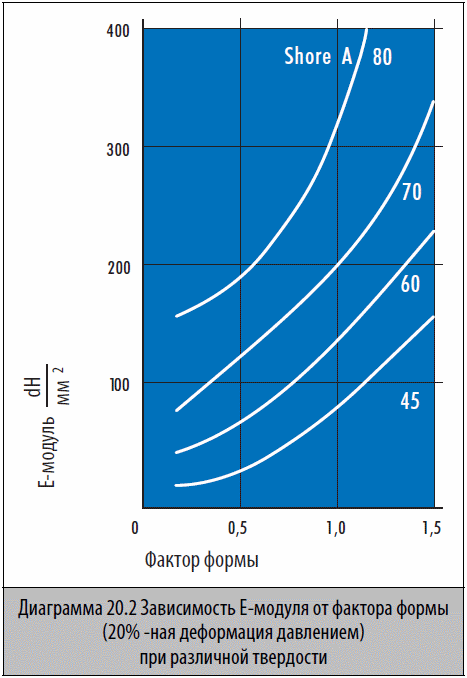 "Единственного" модуля упругости для резино-эластичных материалов, о котором постоянно спрашивают, не существует! |
• Предел прочности при растяжении и относительное удлинение Эти величины являются только качественными характеристиками для исследования возможности применения и определения срока службы деталей из эластомеров, потому что порядок этих величин достигается на практике в исключительных случаях, только при разрушении деталей. Так, напр., для мембран растяжение вблизи зажимного фланца может достигать очень высоких значений, что может привести к преждевременному разрушению. В таких случаях, описанных в начале этой главы, проблему следует решать не только за счет материала, но и за счет изменения конструкции. Значения предела прочности и относительного удлинения, определенные по DIN 53 504, используются для сравнительной характеристики материалов, для их идентификации и производственного контроля, а также для определения устойчивости против разрушающих влияний (агрессивные среды, старение).
• Сопротивление разрыву по надрыву Дополнительную информацию можно получить путем испытания на сопротивление разрыву по надрыву согласно DIN 53 507 и ISO 34-1, для определения усилия сопротивления образца при надрыве в зависимости от толщины образца. Это значение является мерой чувствительности эластомера к разрыву в результате порезов и трещин, не следует его сравнивать с пределом прочности при растяжении. Так как результаты испытаний на разрыв по надрыву значительно зависят от специфических условий испытаний, в особенности, от формы образца, то порядок величин, полученных при лабораторных испытаниях этим методом может не совпадать с данными других методов. Необходимо указывать условия этого испытания и форму образца, например, сопротивление разрыву по надрыву по DIN 53 507, образец B, или сопротивление разрыву по надрыву по DIN 53 515, угловой образец.
|
|
• Упругость и демпфирование Упругость, как и деформация, зависит от температуры, и, прежде всего, от скорости процесса деформирования. Результаты испытания уплотняющих элементов на ударную вязкость по DIN 53 512 не дают основания предсказать эластичные свойства при работе. Часто более целесообразно получить значения упругого восстановления или остаточной деформации в условиях, приближенных к условиям реальной работы. Механическое демпфирование обратно пропорционально упругости. Его можно определить методами, применяемыми для измерения динамического модуля. Тело является упругим, если оно после вынужденной деформации тотчас же снова принимает свою первоначальную форму (напр., стальная пружина). Тело, которое сохраняет свою деформацию, является пластичным, или вязким (напр., пластицированный каучук). Вязкоэластичное тело обладает и тем, и другим свойством, причем у резиноэластичный материала преобладает свойство эластичности. Для вязкоэластичного поведения характерно то, что при упругом восстановлении первоначальное состояние достигается не сразу после снятия нагрузки, а, в зависимости от условий, постепенно. Это свойство имеет значение для уплотняющих элементов и может быть определено при соответствующих лабораторных испытаниях. Вязкоэластичность является единственной причиной специфических физических свойств резино-эластичных материалов. Типичным проявлением вязкоэластичности являются остаточная деформация при испытании на сжатие, релаксация напряжения и ползучесть (→Диаграмма 20.5 и →Диаграмма 20.7). |
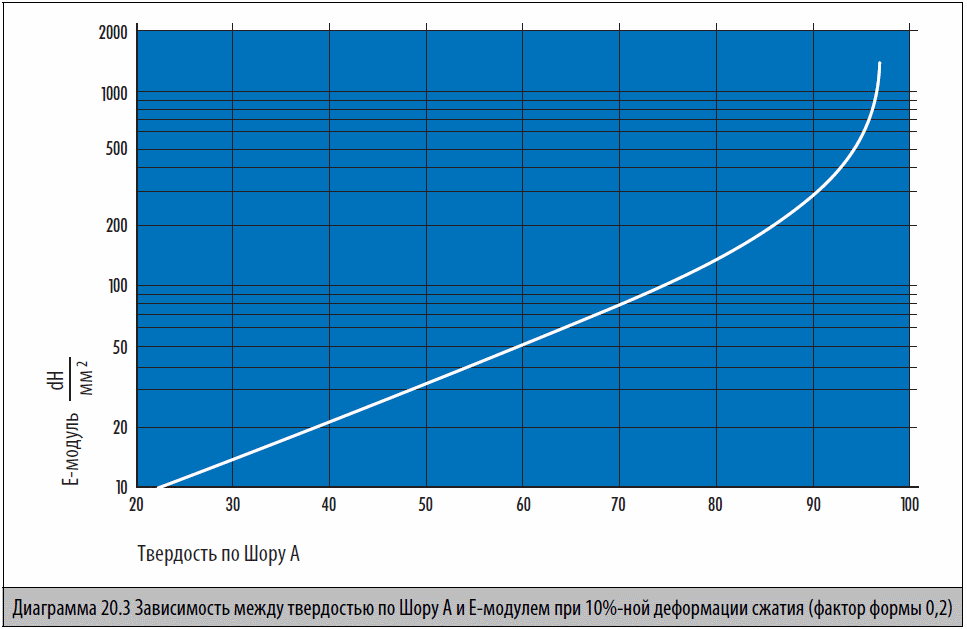 |
• Другие физические свойства В специальных случаях применения могут оказаться важными другие физические свойства: тепловое расширение, антифрикционные свойства, электрические свойства, проницаемость газов и жидкостей. Не будем больше останавливаться на подробностях.
• Температурное поведение Как уже неоднократно упоминалось, температура влияет на физические свойства резиноэластичных материалов очень сильно. Диаграмма →Диаграмма 20.4 показывает зависимость динамического модуля сдвига G от температуры (модуль сдвига измерен при испытаниях на крутильные колебания по DIN 53 445). Справа налево можно увидеть резиноэластичную область с почти постоянным модулем, затем идет переходная область с крутым подъемом и, наконец, область перехода в стеклообразное состояние, в которой резина твердая и хрупкая, снова с почти постоянным модулем. При повторном подъеме температуры хладноломкость снова исчезает. Процесс перехода в стеклообразное состояние является обратимым. Переход из резиноэластичной области в стеклообразное состояние особенно важен, т.к. он во многих случаях определяет границу применения при низких температурах. Этот переход является,
|
|
как видно из диаграммы →Диаграмма 20.4, не резким, а протяженным. Область перехода из резиноэластичного состояния в стеклообразное характеризуется температурой стеклования Ть(температура максимума лог. декремента затухания Λ). Это значение, однако, может дать только грубое представление о низкотемпературном пределе применения материала, так как на практике применение конструкционного эластомерного элемента полностью зависит от вида нагрузки. Один и тот же материал, подверженный ударной нагрузке с очень большой скоростью деформации, достигает предела своего нагружения при более высокой температуре, чем, например, при медленном растяжении. При помощи испытаний на крутильные колебания, действительно, можно дифференцировать различные материалы, но пределы рабочих температур соответствующих конструкционных элементов должны проверяться в условиях, приближенных к рабочим. Пример: У неподвижного уплотнения тепло возникает при начале движении за счет трения. При температурах, когда возникает опасность затвердевания при замораживании, теплоты трения может хватить для сохранения уплотнения упругим или, чтобы привести его в рабочее состояние быстро, сразу после начала движения. |
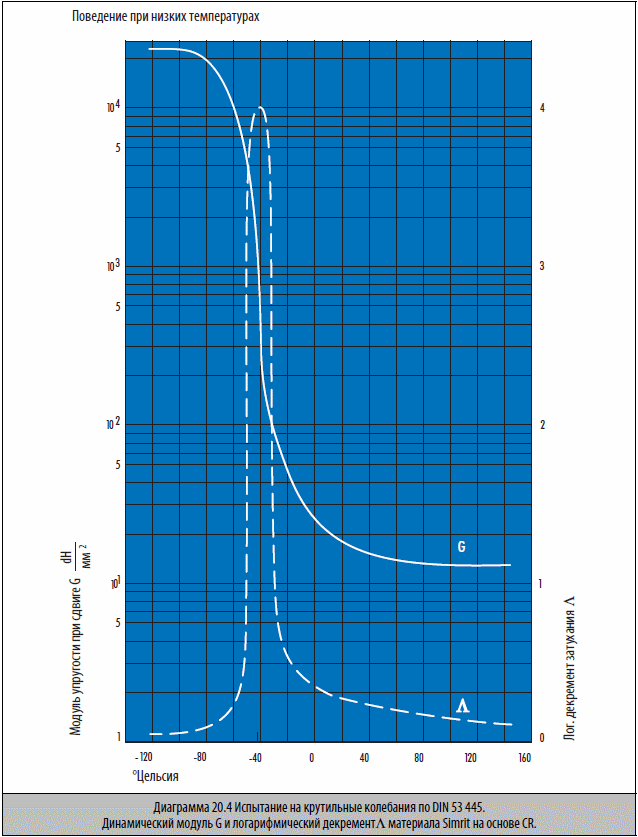 |
Испытания при низких температурах целесообразны только для сравнения материалов и определения их технического применения. Сравнительная оценка материалов по пределу температурного применения, установленному при испытаниях на крутильные колебания, с одной стороны, и полученному из практического опыта, с другой стороны, во многих случаях совпадает. Если низкотемпературный предел одного материала установлен практическим способом (зачастую, с большим трудом), то при помощи значения Tc других материалов можно с уверенностью прогнозировать их поведение при низких температурах в практических ситуациях. Точно так же, как можно провести сравнение между низкотемпературными пределами применения материалов, полученными практическим путем, и температурами перехода в стеклообразное состояние, измеренными при испытаниях на крутильные колебания, можно провести сравнение между ориентировочными значениями низких температур, полученными другими лабораторными методами. Различные методы испытаний могут дать отклонения только до нескольких градусов, и лишь иногда от 30 до 40 Град. При указании ориентировочных низкотемпературных значений обязательно должны приводиться описания методов измерений. Аналогичную процедуру целесообразно применять для описания поведения элементов конструкций на практике. Различные лабораторные методы, используемые для описания поведения при низких температурах, кратко изложены ниже:
• Дифференциальный термический анализ (DTA) Дифференциальная сканирующая калориметрия (DSC)
По этой методике (DIN 3761 Часть 15) маленький образец резины и инертный стандартный образец нагреваются с постоянной скоростью. Снимается график разницы температур между образцом и стандартным образцом в зависимости от температуры. Когда достигается температура перехода в стеклообразное состояние, появляется постоянное отрицательное отклонение, вследствие изменения удельной теплопроводности резины. Точка перехода в стеклообразное состояние на кривой ДТА определяет значение низкотемпературного предела TR.
• Испытание на температурную релаксацию При этом испытании (ASTM D 1329-79) образец резины в виде бруска замораживается в растянутом состоянии в морозильной кювете и снимаются температуры TR 10, TR 30, ... , при которых деформация образца уменьшается на 10, 30, ... процентов.
|
|
• Температура хладноломкости при ударной нагрузке Температура хладноломкости Ts (DIN 53 546) определяется как температура, при которой (при повышении температуры окружающей охлаждающей жидкости) образцы при заданной ударной нагрузке уже больше не ломаются. Таким же образом из относительно простых испытаний можно получить информацию о поведении при низких температурах. Примерами могут служить низкотемпературные испытания на изгиб через оправку при заданных скоростях изгиба или измерение твердости по Шору при различных температурах. В качестве ориентировочного низкотемпературного предела можно установить такую температуру, при которой твердость по Шору составляет 90 пунктов. Ход изменения остаточной деформации при низких температурах дает возможность предсказать низкотемпературную эластичность материала. Так, например, температура, при которой остаточная деформация достигает определенной величины, напр., 50%, может считаться низкотемпературным пределом.
4.2 Устойчивость к среде
Изменения, которые происходят в эластомерных материалах под воздействием окружающей среды и/или условий применения, часто имеют еще большее значение, чем изначальные физические свойства. Поэтому поведение материала должно быть проверено в условиях, приближенных к рабочим.
• Набухание и химическое воздействие При выборе подходящих материалов для уплотнений часто решающими факторами являются химическая устойчивость и поведение при набухании. Поэтому всегда должна иметься информация о жидких и газообразных средах, с которыми контактирует материал. Естественно, температура среды играет решающую роль. Последствия химического воздействия аналогичны последствиям старения под воздействием горячего воздуха, а именно: размягчение или затвердевание, уменьшение прочности, относительного удлинения и эластичности, падение упругости и ползучесть. Кроме того, изменение объема, вызванное набуханием или усадкой, в зависимости от преобладания привноса дополнительного или оттока экстрагированного вещества. Испытания в жидкостях, парах и газах проводятся в соответствии с DIN 53 521 в средах, используемых при эксплуатации, или в стандартных рабочих жидкостях (напр.,в масле ASTM № 1, IRM 902* и IRM 903**, в стандартном топливе ASTM A, B, u C, в испытательном топливе FAM). * заменитель масла ASTM № 2 ** заменитель масла ASTM № 3
|
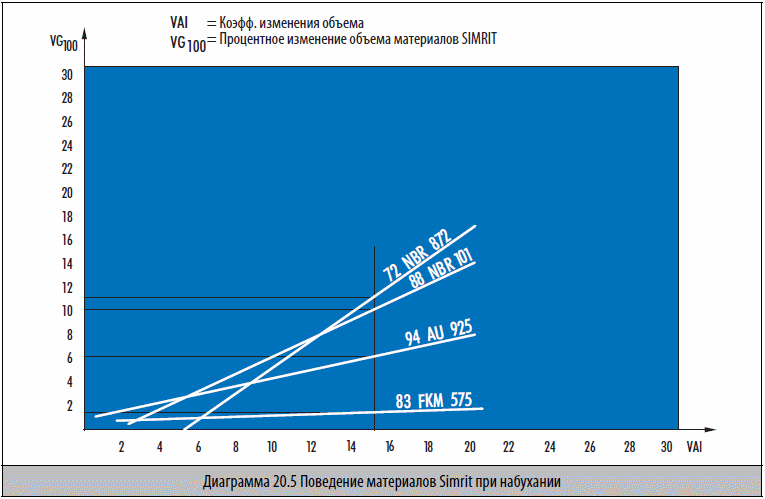 |
• Коэффициент изменения объема Постепенное набухание резино-эластичных материалов в минеральных маслах может быть проверено при использовании стандартных образцов эластомеров. Один из таких стандартных образцов эластомеров из NBR (SRE) уже предложен в качестве тестового материала NBR 1 и прошел стандартизацию согласно DIN 53 538. Изменение объема этого SRE, полученное при стандартных условиях, в любом минеральном масле, обозначается, согласно предложению VDMA, как коэффициент объемного изменения (VAI) исследуемого масла. Если эластомерный материал набухает в любом заданном масле до состояния насыщения, то существует линейная зависимость между объемным изменением эластомера в этом масле и объемным изменением стандартного эластомера (SRE) в том же масле и при тех же условиях, т.е. коэффициент объемного изменения этого масла VAI. Если максимальное изменение объема данного эластомера в масле нанести на график в зависимости от коэффициента изменения объема, то получится прямая линия, которая характеризует поведение эластомера при набухании (QVH). Таким образом, для любого эластомерного материала существует линейная зависимость (QVH). Максимальные изменения объема эластомеров могут быть предсказаны из этих линейных зависимостей |
|
для любого масла, которое имеет известный коэффициент объемного изменения. Эти линейные зависимости уже имеются для некоторых материалов. Используя эти диаграммы, можно комбинировать для конкретного случая применения масло и подходящий материал. Коэффициент объемного изменения (VAI) не дается производителями масел. Пример: в минеральном масле с VAI 15 получены следующие значения изменения объема:
Материалы Simrit |
|
Изменение объема |
83 FKM 575 |
|
1% |
94 AU 925 |
|
6% |
88 NBR 101 |
|
10% |
72 NBR 872 |
|
15% |
• Устойчивость при нагревании, старение Как и все органические химические продукты, резино-эластичные материалы на базе полимеров могут изменяться под воздействием кислорода, воды и/или других сред. В результате этих процессов, называемых старением, такие важные свойства как твердость, растяжение и эластичность могут ухудшиться. Материал может покрыться сетью трещин или разрушиться.
|
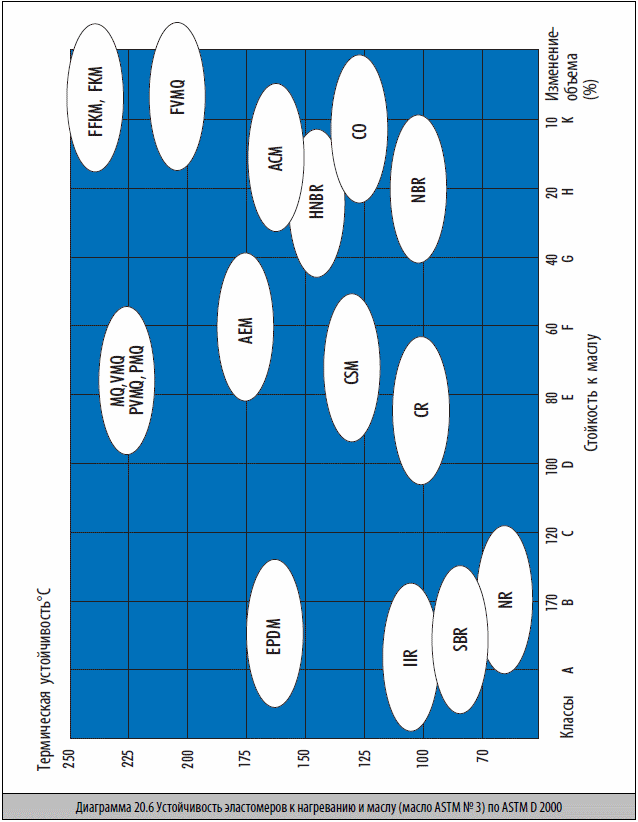
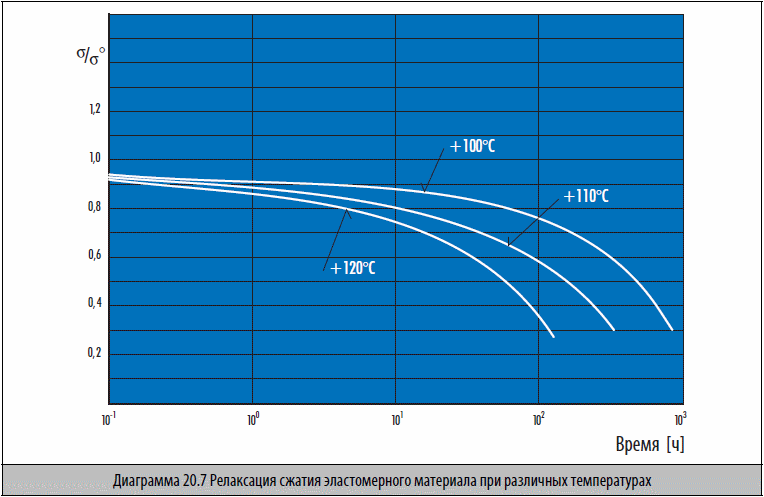
|
Процессы старения ускоряются при нагревании. Освещение и излучение тоже могут привести к разрушениям. Чем выше рабочая температура, тем меньше срок службы детали. Отсюда следуют различные максимально допустимые температуры применения отдельных материалов при кратковременных и постоянных нагрузках. Соответствующие предельные значения, прежде всего, зависят от основного полимера. Процессы старения моделируются за более короткое время испытаний при хранении в термостате (DIN 53 508). Но температура эксперимента и реальная рабочая температура, не должны существенно отличаться. Поведение при старении в достаточной степени характеризуют: изменение твердости, предела прочности при растяжении и удлинения при разрыве, а также остаточная деформация при сжатии или релаксация при нагрузке. Растрескивание деформированных резиновых деталях, подверженных атмосферному влиянию, обусловлена, в основном, присутствием озона в воздухе. Методы проверки устойчивости к озону описаны в DIN 53~509.
• Постоянная статическая нагрузка и деформация Если деталь из резиноэластичного материала на протяжении определенного времени подвергается деформации, параметры которой сохраняются постоянными, то после снятия деформации сохраняется определенная деформация. Установленная испытанием под давлением по DIN ISO 815 и указанная в% от исходной деформации, эта остаточная деформация называется «остаточной деформацией сжатия» (compression set). Остаточная деформация сжатия сильно зависит от температуры и продолжительности деформации. При пониженных температурах преобладают вязко-эластичные процессы, в то время как при повышенных температурах – старение (подробнее → объяснение в DIN ISO 815).
|
|
В определенных случаях остаточная деформация сжатия может быть связана с работой уплотняющих элементов, напр., колец круглого сечения. Текучесть, степень вулканизации и термостойкость – все это оказывает влияние на результаты испытаний. Поэтому лучше измерять релаксацию напряжения сжатия (DIN 53 537), т.к. она дает прямое значение уменьшения контактного давления со временим для уплотнения, постоянно подвергающегося деформации. Если резиноэластичные детали постоянно подвергаются нагрузке, а не постоянной деформации, их деформация увеличивается со временем. Тогда говорят о ползучести. Остаточная деформация сжатия, релаксация напряжения и ползучесть – все эти явления вызваны одними и теми же причинами.
Если температура испытаний основного полимера ниже максимально допустимой рабочей температуры, то релаксация сжатия и ползучесть изменяются во времени по логарифмическому закону, т.е. через определенный промежуток времени они приходят практически к постоянному значению.
• Динамическая нагрузка. Усталость и охрупчивание Разрушение резиновых деталей гораздо чаще связывают с динамической нагрузкой, чем с единичным превышением пределов прочности или растяжения. При постоянной и повторяющейся деформации материал разрушается от внутреннего трения, которое вызывает появление мелких трещин, трещины растут и, наконец, происходит разрушение материала. Стандартные методы испытаний установлены в DIN 53 522 и 53 533.
• износостойкость Это свойство, важное при нагрузке трения, также во многом зависит от условий работы, таких как вид смазки, материал и шероховатость контртела, скорость перемещения, пробуксовывание, контактное давление и температура. Испытания на износ поэтому следует проводить только с готовым продуктом и в условиях, приближенных к реальным условиям работы.
|
 |